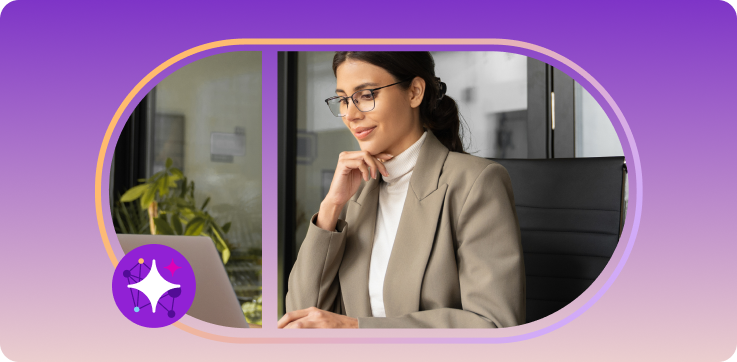
In pharmaceutical research, Batch Manufacturing Records (BMRs) and Batch Production Records (BPRs) are critical aspects of drug discovery and development. These documents capture the detailed processes that ensure the safety, efficacy, and quality of pharmaceutical products.
By thoroughly documenting every step of the manufacturing process, BMR and BPR not only ensure compliance with regulatory standards but also facilitate continuous improvement and innovation. Understanding these records is key to appreciating their role in advancing medical science and improving patient outcomes.
This blog post will aim to provide an understanding of both by looking into the background of BMR and BPR and highlight how they contribute to the advancement of medical science.
BMR: Batch Manufacturing Record: Ensuring Process Consistency and Quality
BMRs are essential to maintaining the consistency and quality of pharmaceutical products. BMRs document every step in the manufacturing process, ensuring that each batch is produced according to strict specifications and regulatory requirements.
BMRs serve as a critical tool for traceability and quality assurance, providing a complete history of how a product was manufactured, from raw materials to final product. This comprehensive documentation allows manufacturers to track deviations, ensure compliance with Good Manufacturing Practices (GMP), and guarantee product safety.
Key aspects of BMR include:
- Process Documentation: Every step in the manufacturing process, including raw material usage, equipment settings, and environmental conditions, is meticulously recorded.
- Compliance Tracking: BMRs help ensure that each batch complies with regulatory standards, minimizing the risk of product recalls or compliance issues.
- Deviation Handling: If any deviations occur during production, they are documented and addressed in the BMR to ensure corrective actions are taken.
BPR: Batch Production Record: From Documentation to Delivery
BPRs complement BMRs by providing detailed documentation of the production activities that occur during manufacturing. BPRs ensure that all steps taken to produce a batch of a product are captured, reviewed, and approved before the product is released to the market.
BPRs offer visibility into the production process, serving as the final verification that all procedures were followed as required. This documentation ensures that each product batch meets quality standards and can be traced back in case of an audit or investigation.
Key aspects of BPR include:
- Production Details: All relevant production activities, such as material quantities, processing times, and equipment usage, are recorded in the BPR.
- Quality Control: The BPR captures results of in-process testing and inspections, ensuring that quality control is maintained throughout production.
- Final Approval: Once the BPR is complete, it must be reviewed and signed off by quality control and production teams before the batch is released.
The Dynamic Connection Between BMR and BPR
BMRs and BPRs work together to ensure the integrity of the manufacturing process and the final product. BMRs provide detailed insights into how each batch is made, while BPRs capture the actions taken during production. Together, they create a robust system for traceability, compliance, and quality control.
This collaboration between BMR and BPR is crucial for maintaining regulatory compliance and ensuring that every batch produced meets the required standards. BMRs help identify potential issues in the production process, while BPRs verify that all steps have been followed correctly before the product reaches the market.
By working in tandem, BMRs and BPRs reduce the risk of errors, improve product consistency, and support the overall goal of delivering safe and effective pharmaceutical products to patients. This combined system strengthens quality assurance and helps manufacturers stay audit-ready, ensuring compliance with industry regulations and enhancing patient safety.
The Impact of BMR and BPR on Healthcare
BMR and BPR also play a crucial role in healthcare by ensuring the consistent quality and safety of pharmaceutical products. These records document every step of the manufacturing process, providing traceability and compliance with regulatory standards.
One of the most significant contributions of BMRs and BPRs to healthcare is their role in preventing errors and ensuring product consistency. By thoroughly documenting each batch’s production process, these records help identify and address any deviations that could compromise product quality. This meticulous documentation ensures that patients receive safe, effective, and reliable medications.
BMRs and BPRs are also vital in facilitating quick and accurate responses to any issues that arise post-production, such as product recalls or adverse events. The detailed records allow pharmaceutical companies to trace issues back to their source, enabling swift corrective actions and minimizing risks to patient safety.
The use of BMRs and BPRs contributes to reducing healthcare costs by ensuring that only high-quality products reach the market. By preventing costly errors and minimizing the need for rework or recalls, these records support more efficient manufacturing processes and ultimately help lower the costs associated with drug production.
BMRs and BPRs have a profound impact on healthcare by ensuring the quality, safety, and efficacy of pharmaceutical products. Their role in maintaining a high level of manufacturing standards directly contributes to better patient outcomes and a more reliable healthcare system.
BMRs and BPRs: Driving Quality in Pharmaceutical Manufacturing
BMRs and BPRs are indispensable tools that ensure the quality, safety, and efficacy of drugs from development to distribution. By documenting every step of the manufacturing process, BMRs and BPRs not only help organizations meet compliance with regulatory standards but also drive continuous improvement and innovation in drug production.
The connection between BMR and BPR is instrumental to advancing medical science. Insights gained from BMR help identify novel drug targets, while BPR ensures these innovations are translated into safe and effective therapies. Together, they form the backbone of a reliable pharmaceutical supply chain, contributing to improved patient outcomes and more efficient healthcare delivery.
As the pharmaceutical industry continues to evolve, the importance of effective documentation and quality control through BMRs and BPRs will only grow. These records are the foundation upon which patient safety and healthcare innovation are built.
By leveraging electronic quality solutions to manage and optimize BMRs and BPRs, pharmaceutical companies can remain at the forefront of innovation, ensuring that they continue to meet the highest standards of quality in an ever-changing regulatory landscape.
Get in touch with us for a demo today and learn about how electronic quality solutions are enabling the industry to remain innovative.