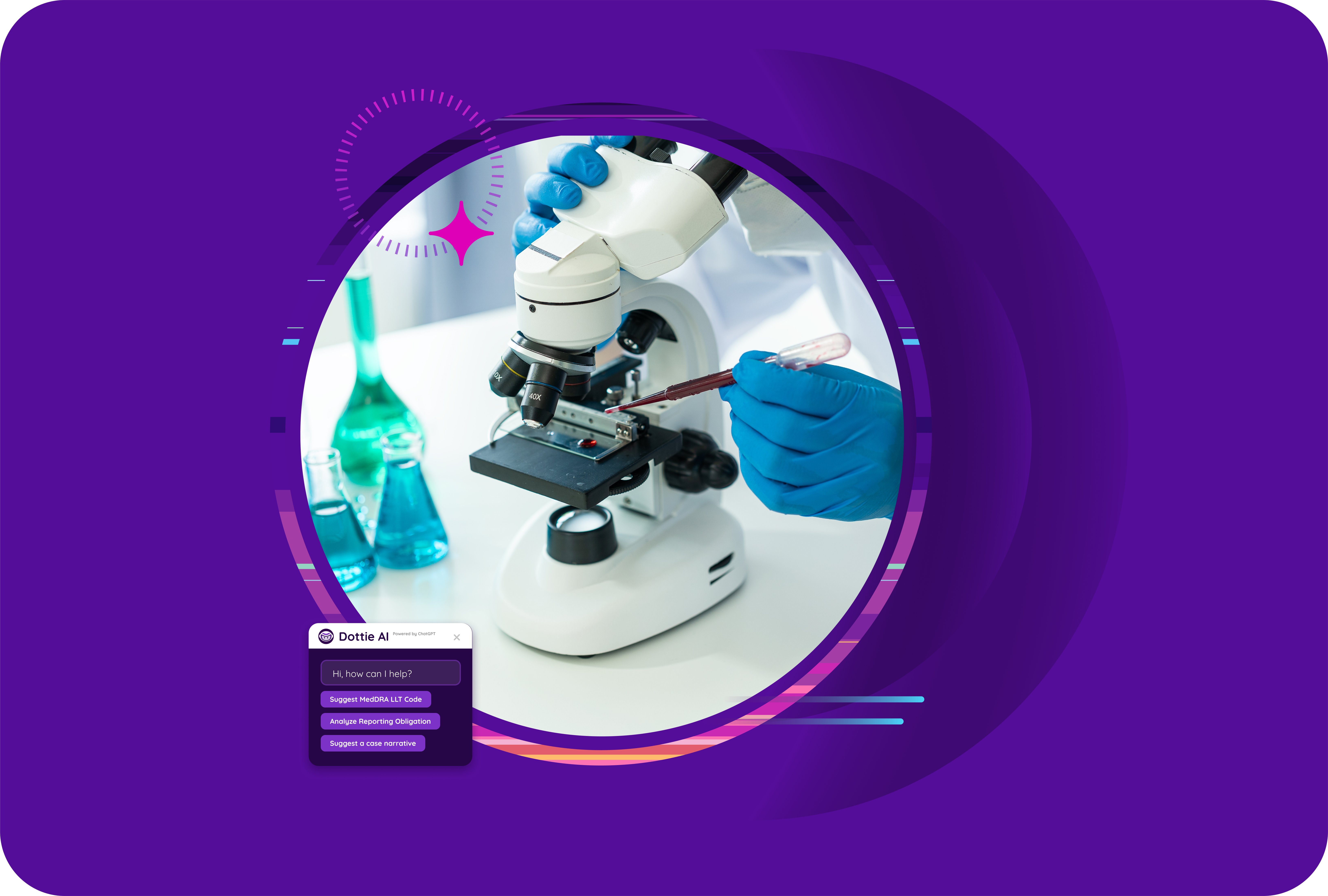
Training management is a crucial part of any medical device manufacturer’s required QMS implementation. A digital QMS can help an organization ensure compliance, deliver quality products to patients, and document all processes and progress. Automating training management can streamline the process for everyone involved while archiving all documentation for easy access.
Outdated training management tools and technology may be costing your firm unnecessary time and money. Paper-based processes can be difficult to assign, track, and manage to completion. By automating employee training, a medical device manufacturer can easily initiate, supervise, and finalize the workflow from a single dashboard. This provides a single source of truth for all stakeholders, including suppliers, customers, and employees.
A closed-loop QMS system can be integrated with a firm’s training process, offering the key to scalable growth in the medical manufacturing industry. Implementing a QMS training management system can streamline the entire process and the result is a more highly trained workforce while meeting regulatory compliance. Below are five essential reasons why you need to implement training management as part of it.
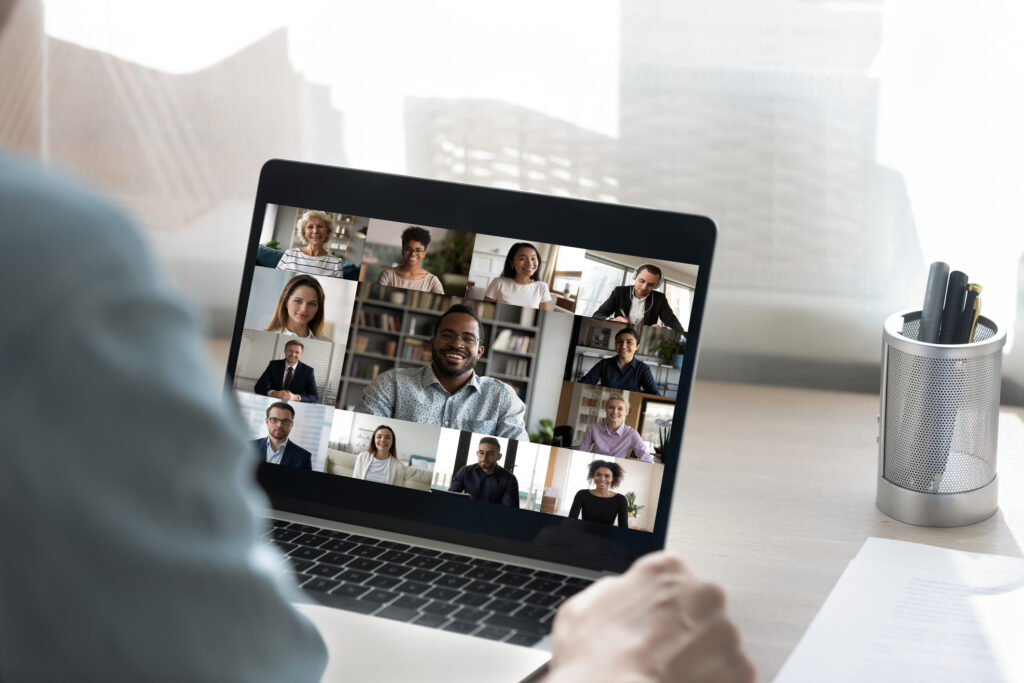
1. Regulatory Requirements
The FDA requires medical device manufacturers to define and document how they met all regulatory requirements. A digital QMS can streamline the process while archiving all such documentation, so it’s available when needed. A QMS also provides employee training or required documentation on demand, with minimal disruption to day-to-day operations.
Key Regulations and Industry Standards Documented by QMS
- Good Manufacturing Practices (GMP) are systems to ensure that products are consistently produced and controlled according to quality standards. They are designed to minimize risks involved in any pharmaceutical production that cannot be eliminated through testing the final product. The GMP compliance requirements for medical devices are outlined in the Code of Federal Regulations (CFR), most prominently in the FDA Quality System Regulations of 21 CFR Part 820.
- The Medical Device Reporting (MDR) regulation (21 CFR Part 803) contains mandatory requirements for manufacturers, importers, and device user facilities to report certain device-related adverse events and product problems to the FDA.
- ISO 9001 sets out the criteria for a quality management system and is the only standard in the family that can be certified to. Checking that the system works is a vital part of ISO 9001.
- The Medical Device Single Audit Program allows an MDSAP recognized Auditing Organization to conduct a single regulatory audit of a medical device manufacturer that satisfies the relevant requirements of the regulatory authorities participating in the program.
2. Dependable Document Control
Standard Operating Procedures (SOPs) can only be effective when everyone in an organization is on the same page. Automating the QMS process ensures uniformity and document control, ensuring clear communication from the top-down.
- Manage the entire lifecycle of documents and content – including version control, lifecycle management, annotations, revisions, electronic signatures, and sharing.
- Enable cross-organizational collaboration and easy editing.
- Ensure the ability to read and understand training management, including direct selection of audience and applicable exams.
- Facilitate binder management that includes revision of documents and records.
It maintains clear and accessible training records, whether general (GMP, safety, company policies) or job-specific (departmental, SOPs, work instruction, or defect identification). Medical device manufacturers must maintain documented records not only of training, but also of product design, complaints, and validation tests.Therefore it is imperative that medical device companies have automated systems that integrate training management with document control to:
3. Holistic View with a Single-Source System
With a holistic QMS training management system, a medical device manufacturer can train all employees from a single source of truth, regardless of job title or geographic location. With such an efficient process, all stakeholders can receive timely updates regarding customer needs and production time, supplier deliveries, inventory control, purchasing, and more.
A holistic QMS solution can manage end-to-end employee training from record management to course distribution and completion to escalation. This empowers organizations to create and deliver specialized content to key stakeholders and collaborative parties. Best practices dictate that a training solution should also integrate with other eQMS core processes to ensure quality and compliance enforcement across the entire ecosystem.
4. Integral ISO & Crucial Certifications
A digital QMS training management system simplifies compliance for your organization while demonstrating to regulatory agencies its ability to consistently produce quality products (per ISO 13485). Integration of a digital QMS ensures that all personnel are trained and ready to handle assigned tasks.
5. Stay Safe and Protect your Bottom Line
A medical device manufacturer must ensure that all employees are properly trained in Occupational Safety and Health Administration (OSHA) and liability management standards and practices. Integrating company-wide OSHA training (among other industry standards) with other quality and compliance processes not only helps save time and money, but also ensures that products are manufactured and delivered in the safest manner.
Conclusion
Training management is a crucial part of any medical device manufacturer’s required QMS implementation. By investing in a cloud-based QMS system to streamline and automate training management with all other processes, medical device manufacturers demonstrate their commitment to safety for employees, stakeholders, and most importantly, patients.
Effective workforce training helps employees in a wide range of roles improve day-to-day productivity. When company-wide training is integrated with a comprehensive QMS, processes and practices are optimized – unlocking scalable growth for medical device manufacturing firms both large and small.