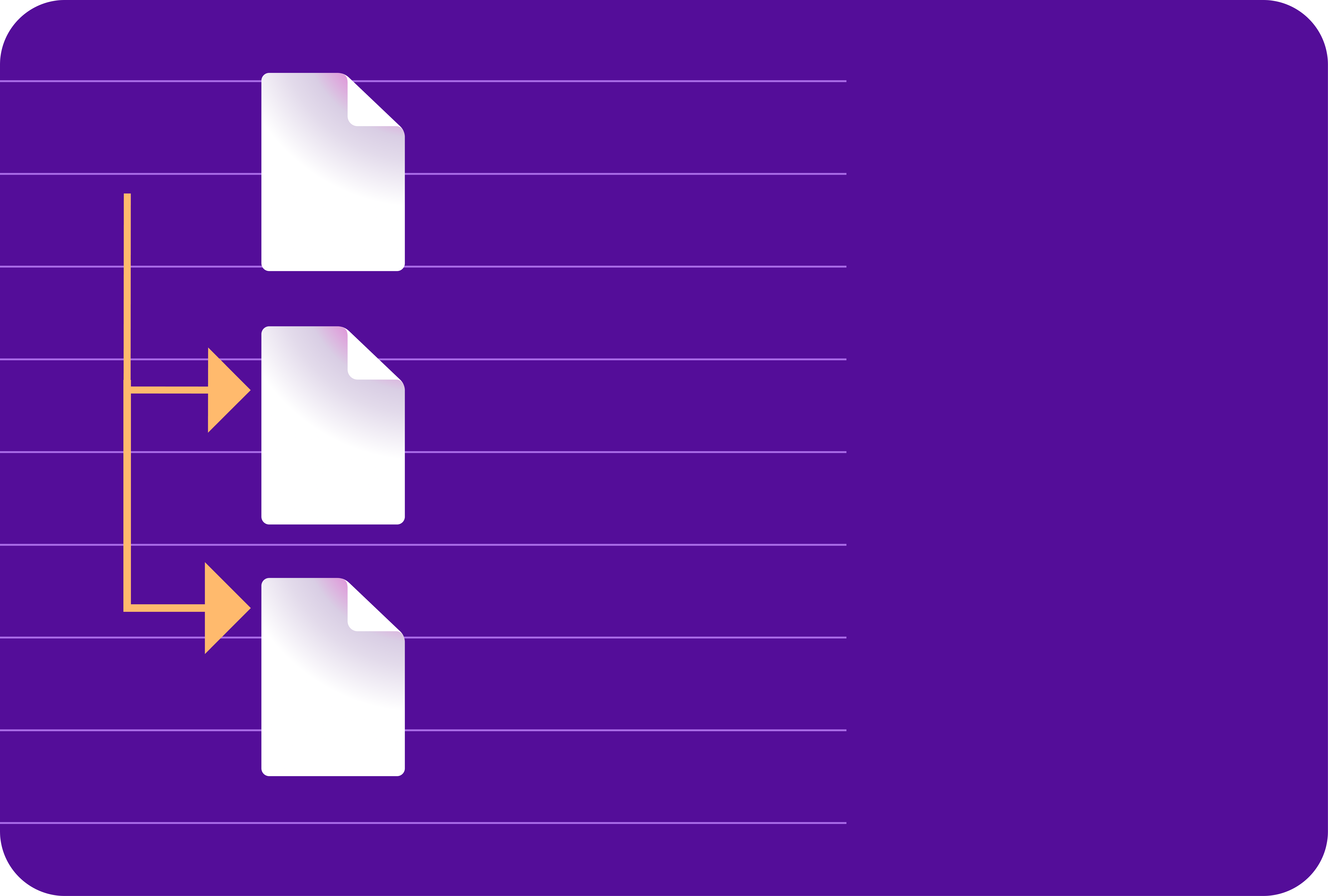
How the ever-changing technology world can easily leave your business behind
According to a recent study, the global Life Science market hit nearly $50 billion in 2019. It is targeted to approach $100 billion by 2027. That adds up to a compelling Compound Annual Growth Rate (CAGR) of 8.5% from 2020 through 2027. However, all CAGR really focuses on is sales. Changing regulatory requirements, technological advancements, and even societal behavioral norms makes the Life Science QMS lift pretty significant. This is rendering traditional QMS solutions obsolete.
The question is, how does a traditional QMS fail in covering the ever changing landscape of our Life Science world?
Now is the time to embrace technology. It’s time to ditch paper processes as well as legacy QMS systems that no longer suit the business needs of today. Tech innovations will streamline your processes, enhance efficiency, and help you meet your growing need for compliance adherence. It does all this without getting tangled in a web of complex, expensive and lengthy deployments. Here are five ways traditional models just don’t compare to modern options.
1) Isolated quality control
A dedicated team assessing quality might seem like a solid way to get unbiased assessments. However, a dedicated team can have trouble keeping up with rapidly changing technology. You can reach short and long term goals much easier if your entire team collaborates. This maximizes not only quality, but also operational efficiencies and regulatory compliance. Traditional QMS waits to assess. Modern QMS continually assesses. In fact it integrates the quality management process throughout the life cycle of everything you do. This allows different perspectives and experiences to be integrated into the quality of your system, therefore producing far superior results.
2) Restricted document control
Paper-based processes—Excel and Word—have been the standard for decades and are an embedded part of the processes for many organizations. These processes are familiar and comfortable for many Life Science manufacturers. At the same time they are more labor intensive, time consuming, and prone to human error. They also require people to be in a physical location to manage and review processes. And, in today’s changing world – especially due to COVID-19 – , where remote working is becoming the norm, having a paper based system that requires team members to be in a specific physical location is not sustainable or cost effective. In addition, paper-based processes are managed separately from the other quality processes in the organization, further perpetuating a siloed organization.
3) People are the “problem” not part of the solution
Traditional QMS focuses on who needs to be held accountable for the failure of a product, a deviation in the manufacturing process, or a regulatory infraction. Whether it is a failure to perform by an employee or a procedural breakdown, traditional QMS often lays the blame on an individual.. More often than not it doesn’t even address the root cause of the problem. An automated, cloud-based QMS allows the entire team to collaborate and provides an electronic history of such collaboration. An automated solution fosters a culture of collaboration that not only improves and streamlines leads, but also creates a more cohesive and higher functioning team.
4) Until it breaks there is little you can do
Waiting is the key word. You are waiting for something to break. Waiting to know if something can be improved. Again, waiting until things are completed before assessing anything, good or bad. Not only does this form a natural queue of problems that need solving, it also leads to the reproduction of flaws. Of course, no company wants a recall or to have to fix deviations. CAPAs, complaint handling, and audits all take time and cost money. However, with the technology available today, organizations of every size can benefit from an integrated QMS that eliminates those issues. Your QMS is engaged at every point of development and can correct inefficiencies, eliminate waste, and implement improvements during every phase of the process.
5) Collecting data can be a nightmare
Results–high quality results–are what every business shoots for. Figuring out whether or not you have achieved those results can be a nightmare in a traditional QMS. Assembling all the data from all the sources takes time and energy. This leads to a tremendous waste of resources (time and money.) Integrated systems allow you to pull result-oriented data at any point during the development process. Reports and analysis are easily created, allowing you to make adjustments, improvements, or see successes as they are happening, almost in real-time.
Bottom line – traditional QMS methods are detrimental to a company’s health. Keeping down costs, reducing overhead, eliminating errors, and building a more cohesive team are more important than ever. Traditional QMS (either legacy solutions or paper-based ones) work against those goals. If you take quality management seriously and want to ensure you stay ahead of, not just keep up with, regulations and best practices it is time to upgrade to a modern, more efficient QMS solution.
If this article has piqued your interest and you want to learn what Dot Compliance can do for, request a demo today.