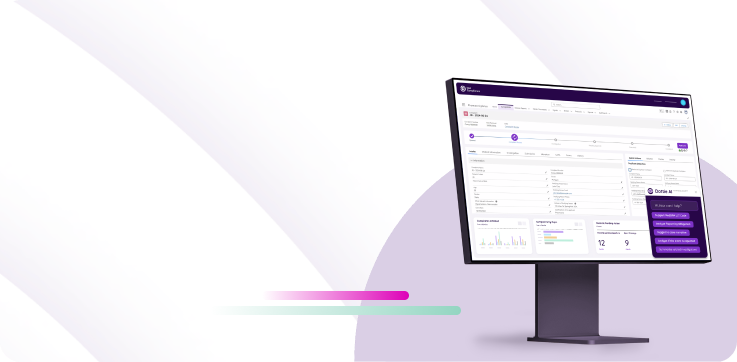
In the life sciences industry, the quality management system (QMS) ensures that all processes, from development to distribution, meet the required standards set by regulatory bodies and industry guidelines. It plays a crucial role in maintaining product safety, effectiveness, and reliability.
The QMS also directly addresses patient needs, ensuring that the products delivered are not only compliant but also trustworthy. By adhering to these standards, companies maintain regulatory compliance and build confidence in their products.
This blog post will explore the key components of a QMS, how it supports compliance and risk management, and its role in maintaining product quality throughout the lifecycle.
We’ll also examine real-world implementations and the impact of technology on enhancing QMS effectiveness.
The QMS Framework: A Closer Look
At its core, a QMS is a comprehensive system comprising interconnected policies, procedures, and processes that guide a company’s operations. It’s a systematic approach to managing quality throughout the entire product lifecycle, from research and development to manufacturing, distribution, and post-market surveillance.
A QMS is built on several foundational elements that work together to ensure consistent product quality and regulatory compliance. These components provide a structured approach to managing and improving quality throughout the organization.
Below are the key elements that form the backbone of an effective QMS.
- Quality Policy: The quality policy sets the foundation for the organization’s commitment to quality. It outlines the company’s goals, objectives, and principles related to quality, serving as a guide for all quality-related decisions and actions. This policy must be clearly communicated and regularly updated to stay aligned with regulatory changes and business needs.
- Quality Planning: Quality planning involves setting specific quality objectives and developing strategies to achieve them. It includes resource allocation, process design, and risk assessment to ensure that all aspects of production contribute to meeting quality standards. Effective planning ensures the organization is prepared to meet its quality goals consistently.
- Quality Assurance (QA): QA focuses on building quality into products from the start. It involves creating and following standard operating procedures (SOPs), conducting audits, and ensuring that processes are consistently applied. QA helps prevent quality issues before they arise, ensuring compliance and reducing the risk of defects.
- Quality Control (QC): QC involves monitoring and testing products during the manufacturing process to ensure they meet specified requirements. This includes inspections, testing, and the use of control charts to detect and correct defects. QC ensures that only products that meet quality standards reach the market.
- Quality Improvement: Quality improvement is the ongoing process of enhancing the QMS to achieve better performance and higher quality outcomes. It involves continuously refining processes, adopting new technologies, and implementing industry best practices. This commitment to improvement helps organizations stay competitive and ensure their products meet or exceed regulatory and customer expectations.
The Critical Role of QMS in Life Sciences
The life sciences industry operates under a microscope, subject to strict regulations due to the potential health risks associated with its products.
Areas a QMS can help include:
- Regulatory Compliance: A QMS helps organizations meet regulatory standards like GMP, GLP, and GCP by providing a structured approach to maintaining compliance. It ensures processes are documented, controlled, and reviewed, reducing the risk of noncompliance.
- Patient Safety: Ensuring patient safety is at the core of the life sciences industry. A QMS enforces quality checks at every stage of the product lifecycle, ensuring that only safe and effective products reach the market, thereby protecting patients from harm.
- Product Quality: Consistency in product quality is critical. A QMS maintains this consistency by overseeing quality control and assurance processes, ensuring that every product meets the required specifications and performs reliably in real-world conditions.
- Risk Management: The industry is full of risks that can affect product quality and safety. A QMS identifies, assesses, and mitigates these risks, preventing issues before they arise and ensuring a quick response when problems occur.
- Brand Reputation: A strong QMS supports a company’s reputation by ensuring products meet high standards of quality and compliance. This builds and maintains customer trust, which is crucial for long-term success and brand loyalty.
Taking a Strategic Approach to Implementing a QMS
Implementing a QMS is a process that requires careful planning and execution. Here are some key steps:
- Needs Assessment: Identify the specific needs and requirements of your organization.
- Documentation: Develop a comprehensive set of policies, procedures, and work instructions.
- Training: Provide training to employees on the QMS and their roles within it.
- Implementation: Roll out the QMS across the organization.
- Monitoring and Review: Continuously monitor and review the QMS to ensure its effectiveness.
Core QMS Technology
In today’s digital landscape, technology significantly enhances the effectiveness and efficiency of QMS in the life sciences industry. Electronic Quality Management Systems (eQMS) offer robust tools that streamline processes, improve compliance, and ensure that quality standards are consistently met across the organization. These systems go beyond basic documentation and process management, providing comprehensive solutions that address all key aspects of quality management.
- Centralized Documentation: Store and manage all documents in one digital repository, ensuring easy access to the most current versions.
- Automation: Automate tasks like document control, CAPA management, and audit scheduling to reduce manual effort and errors.
- Data Analysis: Use real-time data analysis to track quality metrics and identify trends for informed decision-making.
- Integration: Connect eQMS with ERP, CRM, and other systems for seamless data exchange and alignment with organizational goals.
- CAPA Management: Streamline the entire CAPA process with automated workflows, from issue identification to resolution.
- Document Control: Ensure accurate, up-to-date documents with version control, automated approvals, and secure access.
- Training Management: Track employee training, manage certifications, and ensure compliance with training requirements.
- Audit Management: Automate audit scheduling, track findings, and manage follow-up actions for consistent compliance.
- Risk Management: Identify, assess, and mitigate quality risks using integrated risk management tools within the eQMS.
- Change Management: Manage changes with structured workflows, ensuring proper review, approval, and documentation.
Closing Thoughts: The Importance of QMS in Life Sciences
The QMS is an essential component within the life sciences industry. It ensures regulatory compliance, patient safety, and product efficacy and manages every stage of product development, from design to post-market surveillance, ensuring all processes meet regulatory standards. This approach prevents recalls, maintains compliance, and builds trust with patients and healthcare providers.
The QMS also drives innovation and strengthens a company’s reputation. By managing quality systematically, companies can streamline processes, reduce costs, and improve product performance, gaining a competitive edge. A commitment to quality fosters long-term relationships with customers and partners.
Ultimately, a QMS helps meet regulatory requirements and contributes to the well-being of millions of patients who rely on life sciences products.
Now that you know what a QMS is and why it’s important, learn the steps to choosing the best solution for your company.
Download this free white paper for your step-by-step guide.