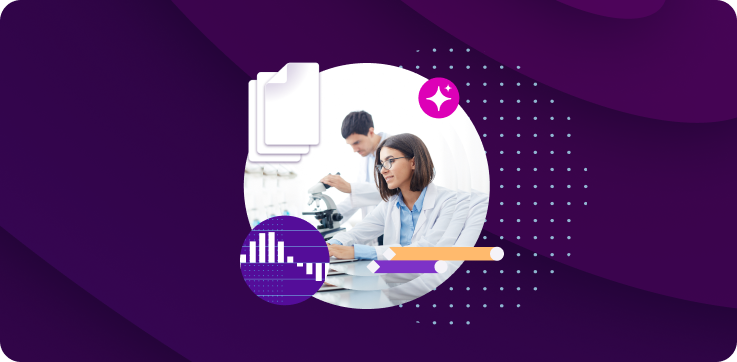
Ensuring a high level of quality is essential for success in any industry. With the level of regulatory scrutiny that companies face, along with customer expectations, and the complexity of products and services, organizations must excel in all operations to stay ahead. Electronic Quality Management Systems (eQMS) help meet these demands by streamlining processes, helping to meet compliance, and supporting continuous improvement across the enterprise.
This blog post will consider the critical elements of an eQMS, exploring its core components, benefits, and considerations for implementation.
Read on to learn how organizations can use the eQMS to accelerate growth in today’s demanding market.
What’s It Made Of? Under the Hood of the eQMS
An eQMS is designed to centralize and automate various aspects of quality management, providing a comprehensive platform for organizations to streamline their processes, enhance compliance, and drive continuous improvement.
An effective eQMS encompasses the following key components:
Document Management
- Centralized repository: Store all quality-related documents, including procedures, work instructions, specifications, and quality plans, in a single, easily accessible location.
- Version control: Track document revisions, ensuring that only the most up-to-date versions are used and that historical records are maintained for auditing purposes.
- Workflow automation: Streamline document review, approval, and distribution processes, reducing manual effort and ensuring timely dissemination of critical information.
Nonconformance Management
- Incident reporting: Facilitate the timely reporting and investigation of nonconformities, deviations, and complaints.
- Root cause analysis: Use advanced tools to identify the underlying causes of quality issues, enabling organizations to implement targeted corrective actions.
- Corrective and preventive action (CAPA) management: Track and manage CAPA plans, ensuring that effective measures are implemented to prevent the recurrence of problems.
Audit Management
- Audit planning: Create and manage audit schedules, assign auditors, and distribute audit checklists.
- Audit execution: Conduct audits efficiently, capturing evidence and documenting findings.
- Audit reporting: Generate comprehensive audit reports, highlighting key findings, recommendations, and corrective actions.
Training Management
- Training plan creation: Develop and manage training plans that align with organizational needs and regulatory requirements.
- Training record management: Track employee training records, certifications, and expiration dates.
- Compliance monitoring: Ensure that employees receive necessary training to meet regulatory mandates and maintain competency.
Risk Management
- Risk identification: Identify potential quality risks and assess their likelihood and impact.
- Risk assessment: Evaluate the severity of identified risks and prioritize them based on their potential consequences.
- Risk mitigation: Develop and implement strategies to mitigate or eliminate identified risks.
Supplier Quality Management
- Supplier evaluation: Assess supplier performance and capabilities to ensure they meet your organization’s quality standards.
- Supplier onboarding: Streamline the supplier onboarding process, including contract negotiation and quality agreement establishment.
- Supplier performance monitoring: Track supplier performance metrics, identify areas for improvement, and address non-conformance issues.
Data Analytics
- Data collection: Gather and store quality-related data from various sources, including production records, inspection results, and non-conformance reports.
- Data analysis: Utilize advanced analytics tools to identify trends, patterns, and correlations within the data.
- Reporting: Generate customized reports and dashboards to provide stakeholders with actionable insights into quality performance.
Integration
- System interoperability: Seamlessly integrate the eQMS with other enterprise systems, such as ERP, CRM, and PLM, to create a cohesive quality management ecosystem.
- Data synchronization: Ensure that data is synchronized across different systems, eliminating manual data entry and reducing the risk of errors.
- Workflow automation: Streamline workflows by automating data transfers and triggering actions based on predefined rules.
What’s In It for You? The Benefits of Implementing an eQMS
Implementing an eQMS provides a variety of benefits that can significantly improve your organization’s operations and bottom line.
Some of these key benefits include:
- Enhanced Efficiency: Automate routine tasks, reduce paperwork, and streamline processes, leading to improved operational efficiency and cost savings.
- Improved Compliance: Meet compliance with regulatory standards and industry best practices, mitigating the risk of noncompliance and associated penalties.
- Enhanced Data Management: Centralize and organize quality-related data, improving accessibility, accuracy, and traceability.
- Improved Decision Making: Leverage data analytics to gain valuable insights, identify trends, and make data-driven decisions.
- Enhanced Customer Satisfaction: Deliver higher-quality products or services, leading to increased customer satisfaction and loyalty.
- Improved Employee Morale: Empower employees with tools and information to effectively manage quality, boosting morale and engagement.
Tips for Choosing the Right eQMS
Selecting the right eQMS is a critical decision that can significantly impact your organization’s success. Consider the following factors when evaluating potential solutions:
- Functionality: Ensure the eQMS aligns with your specific quality management needs and requirements.
- Scalability: Choose a solution that can accommodate your organization’s growth and evolving needs.
- Integration: Verify compatibility with existing systems to avoid disruptions and ensure seamless data flow.
- Cost: Evaluate the initial investment, ongoing maintenance costs, and potential return on investment.
- Vendor Support: Assess the vendor’s reputation, customer service, and commitment to ongoing support and updates.
Use Cases: Potential eQMS Applications in the Real World
To gain a deeper understanding of the transformative impact eQMS can have on organizations, let’s explore some possible scenarios from the perspective of the pharma, biotech, and medical device industries:
Scenario 1: Pharmaceutical Giant Streamlines Quality Processes
Consider this–a leading pharmaceutical company faced challenges in managing its complex quality processes, meeting compliance with regulatory requirements, and maintaining data integrity. By implementing an eQMS, the company can:
- Centralize quality data: Consolidate quality-related information from various sources, improving data accessibility and accuracy.
- Automate routine tasks: Streamline processes such as document management, non-conformance reporting, and audit scheduling, freeing up valuable resources.
- Enhance compliance: Ensure compliance with FDA regulations, including CGMP and 21 CFR Part 11, through automated compliance checks and audit trails.
- Improve traceability: Establish effective traceability mechanisms to track products from raw materials to finished goods, facilitating recalls and investigations.
- Optimize risk management: Identify and mitigate potential quality risks proactively, safeguarding product safety and efficacy.
- Enhance data analytics: Leverage data-driven insights to identify trends, analyze quality performance, and support continuous improvement initiatives.
Scenario 2: Biotech Startup Accelerates Time to Market
Now let’s consider the perspective of a biotech startup. Let’s say this rapidly growing biotech startup struggled to manage its quality processes efficiently, particularly as it scaled up operations and prepared for regulatory submissions.
By adopting an eQMS, the company could:
- Accelerate product development: Streamline quality review and approval processes, reducing time-to-market for new products.
- Enhance regulatory compliance: Comply with Good Laboratory Practices (GLP) and other relevant regulations.
- Improve data integrity: Maintain accurate and reliable data throughout the product development lifecycle.
- Facilitate collaboration: Enable collaboration among teams involved in quality assurance, research and development, and manufacturing.
- Scale efficiently: Support organizational growth by providing a scalable and flexible quality management platform.
Scenario 3: Medical Device Manufacturer Improves Patient Safety
Now we’ll look at the medical device industry. Consider a medical device manufacturer that is facing increasing pressure to ensure the safety and efficacy of its products. By implementing an eQMS, the company could:
- Enhance product quality: Improve product design, manufacturing processes, and testing procedures to minimize defects and risks.
- Strengthen risk management: Proactively identify and mitigate potential safety hazards associated with medical devices.
- Improve traceability: Track medical devices throughout their lifecycle, enabling faster recalls and investigations if necessary.
- Strengthen regulatory compliance: Ensure compliance with FDA regulations, such as Quality System Regulation (QSR).
- Enhance patient safety: Reduce the risk of adverse events and improve patient outcomes through effective quality management practices.
These scenarios demonstrate the potential of eQMS in the pharma, biotech, and medical device industries. By streamlining quality processes, enhancing compliance, and driving continuous improvement, the eQMS can help organizations like these achieve their goals, improve patient safety, and deliver high-quality products to market faster.
See the Difference an eQMS can Make
Organizations need to prioritize quality management to remain competitive, keep customers happy, and meet regulatory compliance. An eQMS provides an effective solution for streamlining quality processes, improving efficiency, and driving continuous improvement. By centralizing quality data, automating tasks, and providing real-time insights, an eQMS empowers organizations to identify and address quality issues promptly, reduce costs, and improve overall performance.
By carefully evaluating factors like functionality, scalability, integration capabilities, and vendor support, you can select the right eQMS to optimize your organization’s quality management efforts and achieve long-term success in today’s demanding market.
Now that you know what an effective eQMS consists of, learn how you can start reaping these benefits.
Download our white paper to learn how to choose the right eQMS for your business.