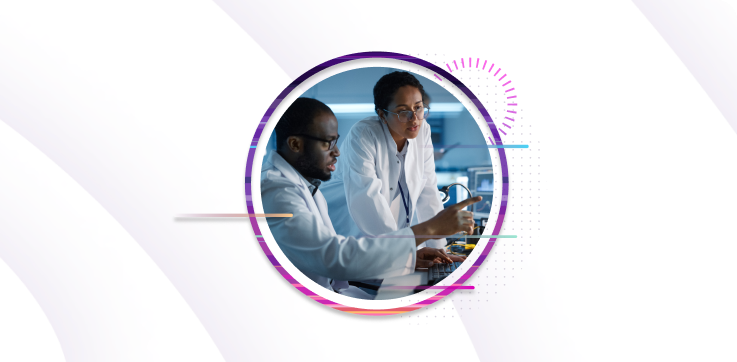
The life sciences industry is highly regulated and patient-centric, making compliance a critical component for all companies involved in the manufacture or distribution of these products.
A quality management system (QMS) enables efficient processes, mitigates risks, and ensures that these products meet the highest regulatory standards.
This blog post will consider the seven essential steps to building an effective QMS tailored to the unique needs of the life sciences industry.
Read on to learn how to incorporate an effective QMS within your organization.
Step 1: Define Your QMS Scope
The first step in establishing a QMS is to clearly define its scope. This involves identifying the products, processes, and activities that will be included within the system.
Consider the following factors:
- Regulatory Requirements: Determine the specific regulations and standards that apply to your products and processes. This may include FDA regulations for medical devices or pharmaceutical products, EMA regulations for products sold in the European Union, or ISO standards for general quality management.
- Product Life Cycle: Define the stages of product development, manufacturing, distribution, and post-market surveillance that will be covered by your QMS. This will help you ensure that all critical aspects of your products are addressed.
- Organizational Structure: Consider the different departments and functions involved in product development, manufacturing, and quality assurance. This will help you identify the key areas that need to be included within your QMS.
Step 2: Conduct a Gap Analysis
Once you’ve defined the scope of your QMS, conduct a thorough gap analysis to assess the current state of your quality management practices. This involves comparing your existing systems and processes against the requirements of your chosen standards. Identify areas where there are deficiencies or opportunities for improvement.
Key areas to focus on during the gap analysis include:
- Documentation and Records: Review your existing documentation and record-keeping practices to ensure they are adequate and compliant with the QMS standard.
- Quality Control: Assess your quality control processes, including testing, inspection, and nonconforming product management.
- Supplier Management: Evaluate your supplier management practices to ensure that your suppliers meet quality standards.
- Employee Training: Review your employee training programs to ensure that staff are adequately qualified and trained.
- Risk Management: Assess your organization’s risk management practices to identify and address potential risks.
- Continuous Improvement: Evaluate your organization’s commitment to continuous improvement and identify areas for improvement.
Step 3: Develop a QMS Documentation Framework
A strong documentation framework is essential for a functioning QMS. Create a comprehensive set of policies, procedures, and work instructions that cover all aspects of your quality management activities.
Consider the following key documents:
- Quality Manual: The overarching document that outlines the scope, objectives, and policies of your QMS. It serves as a roadmap for your quality management activities.
- Standard Operating Procedures (SOPs): Detailed instructions for specific tasks or processes, such as manufacturing, testing, or inspection. SOPs should be clear, concise, and easily understood by all relevant personnel.
- Work Instructions: Step-by-step guides for performing specific activities, such as operating equipment or completing forms. Work instructions should be detailed and easy to follow.
- Forms and Templates: Standardized documents for capturing data and information, such as inspection reports, test results, and nonconformance reports. Forms and templates can help ensure consistency and efficiency in data collection and analysis.
Step 4: Implement the QMS
Once you have developed your documentation framework, it’s time to implement the QMS. This involves training employees, providing necessary resources, and ensuring that the system is followed consistently.
Consider the following activities:
- Employee Training: Provide comprehensive training on the QMS, including policies, procedures, and the use of documentation. Ensure that all relevant personnel understand their roles and responsibilities within the QMS.
- Resource Allocation: Allocate adequate resources, such as personnel, equipment, and facilities, to support the effective operation of the QMS. This may involve hiring additional staff, investing in new technology, or modifying existing facilities.
- Communication: Establish effective communication channels to keep employees informed about QMS updates, changes, and expectations. This can include regular meetings, newsletters, and training sessions.
Step 5: Conduct Internal Audits
Regular internal audits are essential for assessing the effectiveness of the QMS and identifying areas for improvement. Conduct audits to verify compliance with regulations, standards, and internal procedures. Use the audit findings to implement corrective actions and preventive measures.
By conducting regular internal audits, you can:
- Meet compliance: Ensure that your QMS aligns with relevant regulations, standards, and internal procedures.
- Identify nonconformances: Proactively detect and address any deviations from established processes or requirements.
- Continuously improve: Use audit findings to identify opportunities for improvement and implement corrective actions.
Step 6: Continuously Improve the QMS
Quality management is an ongoing process, and the QMS should be continuously improved to address evolving requirements and challenges. Implement a system for identifying and addressing nonconformities and implementing corrective actions. Consider using tools like root cause analysis to identify the underlying causes of quality issues.
Examples of key activities include:
- Implement corrective actions: Develop and implement effective corrective actions to address any identified nonconformances. This may involve changing processes, procedures, or training employees.
- Conduct root cause analysis: Use tools like root cause analysis to identify the underlying causes of quality issues. This can help you implement more effective corrective actions and prevent similar problems from recurring.
- Review and update QMS documentation: Regularly review and update your QMS documentation, including policies, procedures, and work instructions, to ensure that they remain accurate and relevant.
Step 7: Seek External Certification
While not always mandatory, obtaining external certification can provide a valuable validation of your QMS. Consider seeking certification against standards like ISO 9001, ISO 13485, or other industry-specific standards. Certification can enhance your credibility with customers, regulators, and other stakeholders.
Benefits of obtaining external certification include:
- Enhanced credibility: Certification can enhance your organization’s reputation and credibility with customers, regulators, and other stakeholders.
- Improved market access: In some cases, certification may be a requirement for doing business in certain markets or with specific customers.
- Reduced risk: Certification can help reduce the risk of regulatory noncompliance and product recalls.
- Continuous improvement: The certification process can drive continuous improvement within your organization as you strive to meet the requirements of the standard.
Get More from Your QMS
An effective, end-to-end QMS serves as the foundation for ensuring product quality, patient safety, and regulatory compliance. By following the seven steps outlined in this guide, organizations can develop a system that enhances product quality, protects patient safety, and meet regulatory compliance. This comprehensive approach will position your organization for long-term success.
Looking for even more information?
Download the white paper for an in-depth look into how to choose an eQMS.