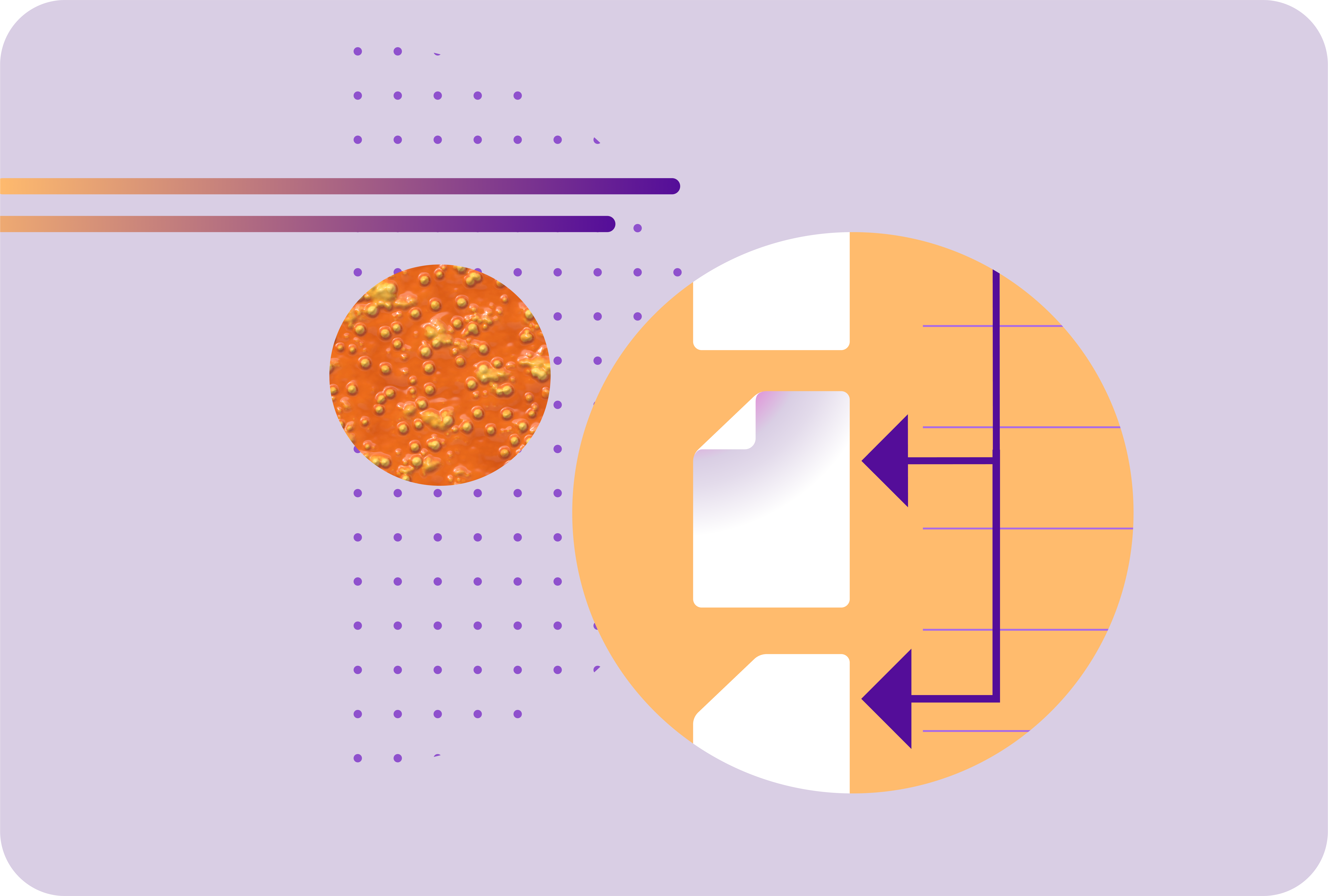
Downloadable to Help Prepare for Your Next Audit (XLS)
The life science industry is built upon a foundation of strict regulations and standards designed to enforce product quality and patient safety. This applies to products as well as services. ISO 13485 represents an essential level of standardization and certification for Quality Management Systems (QMS) in the medical device manufacturing industry. A properly maintained QMS can help medical organizations track, maintain, and improve business processes – just as a certification can help the organization improve quality and pass audits.
ISO 13485 represents the highest stand-alone industry standard detailing requirements for healthcare QMS. These standards help medical device manufacturers meet compliance laws and ensure customer satisfaction. They also protect patients, as well as their physicians at hospitals, private practices, and clinics. Certification by an accredited certifier is not required by all countries but can help establish supplier and patient trust.
Find out: Does my country require ISO 13485 Certification?
Product safety and quality are non-negotiable in the medical device manufacturing industry, and must be reinforced throughout a product’s entire life cycle.This article will examine ISO 13485, what it does and why it is needed, and provide a downloadable ISO 13485 Audit Checklist for your medical device manufacturing QMS to help you towards successful certification.
What is the ISO 13485 Standard?
The ISO 13485 Standards are international regulations set forth by the International Organization of Standardization (ISO) and designed for organizations that design, produce, install, and service medical devices. ISO 13485:2016 is the most current version. It places a greater emphasis on risk-based decision-making and shifting regulatory changes in the supply chain.
These quality standards provide a practical foundation for QMS requirements. They are critically important for all stakeholders in the medical device industry to:
- manage quality standards
- meet QMS compliance regulations
- demonstrate competency and consistency
- meet customer safety and regulatory requirements
Whom does the Standard Apply to?
The ISO 13485 Standards were designed for medical device manufacturers to regulate compliance and quality regarding medical devices, manufacturers, developers, contractors, service providers, distributors, and importers.
ISO 13485 also helps healthcare providers (regardless of size) establish and maintain an effective Quality Management System to protect physicians, healthcare organizations, and patients. These regulations extend beyond a medical product’s development and continue across its entire life cycle. They also affect the medical technology field, suppliers, and other external parties.
The most effective method to comply with ISO 13485 is establishing a QMS and using an audit checklist to aid in certification. A digital QMS tracks, manages, and organizes all internal processes; and can be integrated with existing systems and solutions. This data aggregation and real-time status updates yield the most accurate information possible regarding company processes, billing, and, ultimately, continuous improvement.
Why Get ISO 13485 Certified?
Although not required by every country, a certification can establish a company as more reputable and trustworthy – and increase efficiency and accuracy. ISO 13485 guidelines are international and issued by the International Organization for Standardization (ISO).
There are many benefits to attaining a certification from an accredited organization. An ISO 13485 Standard certification works with a QMS to protect an organization, its patients, and its stakeholders by reducing legal risks, increasing safety, and providing more economical working environments. Healthcare firms with QMS and ISO 13485 certification can harmonize internal regulatory requirements of medical devices and ensure that all systems, operations, and processes are performing at maximum capacity.
ISO audits review processes and procedures of medical device manufacturers. Third-party recertification audits typically occur every three years. A checklist can provide a strategy for a risk-based approach to quality processes, while QMS standards rely upon the iterative approach of Plan/Do/Check/Act. This methodology encourages regular verification, corrective actions, and preventative adjustments moving forward. The systems work together to create a powerful cycle of continuous improvement.
An ISO 13485 checklist built on documented evidence demonstrates proof of compliance and is key to passing any 3rd party medical device single audit program. These internal rules and guidelines document the structure and sequence of:
- business processes
- policies
- procedures
- roles and responsibilities
- forms and templates
When an audit occurs, the completed checklist and QMS documentation serve as evidence of the firm’s compliance.
Get Your Checklist HereWhat Are the ISO 13485Audit Requirements?
ISO 13485 requirements for a QMS apply to all medical device manufacturing organizations and the attached supply chains. The most current version, ISO 13485:2016, emphasizes a risk-based approach, a fundamental requirement for medical device manufacturers. The latest requirements can be obtained from the ISO website.
The ISO standards comprise eight sections. The first three sections introduce the scope, normative references, and definitions, while the remaining sections detail the requirements. Sections four through eight comprise the main sections of the audit and comprised of questions regarding the issues detailed here:
Section Four – Quality Management Systems
General QMS expectations, requirements, and documentation are included in this section, including requirements for the quality manual, medical device file, and control of documents and records.
Section Five – Management Responsibility
Top management must be involved in the implementation and maintenance of the QMS and ongoing reviews. The result is employee faith, customer satisfaction, and continuous internal improvement.
Section Six – Resource Management
Human resources, infrastructure, work environment, and much more are considered key resources and must be managed closely.
Section Seven – Product Realization
Every aspect of a product – its planning phases, requirements reviews, design and development, purchasing, delivery, measurement, any servicing – must be controlled and monitored.
Section Eight – Measurement, Analysis, & Improvement
Data comes from measurement, which is required to maintain a QMS and improve internal processes. QMS functionality can be improved via assessing customer satisfaction, performing internal audits, analyzing non-conformances, improving products and processes, and taking preventative and corrective measures along the way.
Following the ISO 13485 Standards can ensure that all internal processes follow plans and meet regulatory requirements as defined in the QMS.
How to Use Your ISO 13485 Audit Checklist
The ISO 13485 Audit Checklist contains a series of questions and status updates to ensure that everything matches the plans defined in the organization’s QMS regarding internal activities, supplier evaluation, and an evaluation of the supplier audit reports.
The downloadable ISO 13485 Audit Checklist contains twelve tabs that begin with general instructions, then has ten tabs with questions for the areas of auditing, and concludes with a tab to list recommendations, notes, and signatures as needed. Use each of the tabs in chronological order to help ensure your QMS is aligned with ISO 13485 Standards, and determine readiness for a third-party audit.
Make Your ISO 13485 Audit a Success
A successful 13485 audit is critical to any organization involved in the manufacture, distribution, maintenance, and disposal of medical devices. Because these audits are closely linked to quality and consistency, it is vital to utilize a digital QMS to demonstrate proficiency and pass audits.
Dot Compliance offers a cloud-based QMS specifically designed for medical device manufacturers. Request a quote today for a robust, high-quality QMS to help streamline audits and maintain product quality.