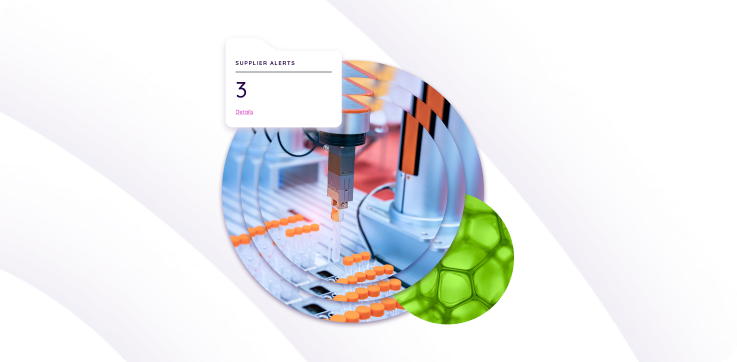
Corrective and Preventive Action (CAPA) plays a key role in maintaining product quality in the pharmaceutical industry, as outlined by the ICH Q10 guidelines. This process addresses quality issues and prevents them from recurring. CAPA is proactive, prioritizing risk, conducting root cause analysis, and fostering continuous improvement.
This blog post covers the key principles of CAPA in ICH Q10, the main components of a CAPA system, and best practices for effective implementation. Learn how, by integrating these elements, companies can ensure compliance and enhance product safety.
The Role of CAPA in ICH Q10: A Deeper Dive
ICH Q10 recognizes CAPA as a fundamental pillar of an effective Pharmaceutical Quality System (PQS). It outlines the principles and practices that pharmaceutical companies should adopt to ensure that their CAPA systems are effective and compliant.
The guideline emphasizes the following key aspects:
Proactive Approach
CAPA should not be viewed solely as a reactive measure to address problems after they occur. Instead, it should be a proactive mechanism for identifying potential risks and taking preventive actions. This proactive approach aligns with the overall goal of continuous improvement and helps to prevent issues before they arise.
Risk-Based Prioritization
CAPA activities should be prioritized based on the risk associated with the nonconformity or issue. This ensures that the most critical problems are addressed first, while less significant issues can be handled in a more timely manner. By prioritizing based on risk, companies can allocate resources effectively and focus on the areas that pose the greatest threat to product quality and safety.
Root Cause Analysis
A thorough investigation is essential to determine the underlying causes of quality issues. This helps to prevent recurrence and identify opportunities for process improvement. Root cause analysis involves delving deeper than surface-level symptoms to uncover the root causes that contribute to the problem. By understanding the root causes, companies can implement targeted corrective and preventive actions that address the underlying issues rather than merely treating the symptoms.
Effective Communication
Clear and timely communication among all relevant parties is crucial for a successful CAPA process. This includes stakeholders from different departments, such as quality assurance, manufacturing, and regulatory affairs. Effective communication ensures that everyone is aligned on the goals of the CAPA process, understands their roles and responsibilities, and is kept informed of progress and updates.
Continuous Improvement
CAPA should be viewed as an opportunity for continuous improvement. By analyzing the root causes of issues and implementing corrective and preventive actions, companies can enhance their processes and reduce the likelihood of future problems. CAPA can help to identify areas where processes can be streamlined, optimized, or made more efficient. By continuously improving their processes, companies can enhance product quality, reduce costs, and improve overall performance.
Key Components of a CAPA System
Look for a CAPA system that includes the following components:
- Issue Identification: Nonconformities, deviations, complaints, or other quality issues should be promptly identified and documented.
- Investigation: A thorough investigation is conducted to determine the root cause of the issue. This may involve interviewing stakeholders, reviewing documentation, and analyzing data.
- Corrective Action: Once the root cause is identified, corrective actions are implemented to address the immediate problem. These actions may include changes to procedures, equipment, or personnel.
- Preventive Action: To prevent recurrence, preventive actions are implemented to eliminate or mitigate the underlying causes. This may involve changes to processes, training, or quality standards.
- Verification and Validation: The effectiveness of both corrective and preventive actions is verified and validated to ensure that they have achieved their intended results.
- Documentation: The entire CAPA process, including investigations, actions, and verification, is documented to provide a record for future reference.
Best Practices for CAPA Implementation
To ensure the effectiveness of a CAPA system, pharmaceutical companies should consider the following best practices:
- Use of Quality Risk Management (QRM): Integrate QRM into the CAPA process to assess the likelihood and impact of potential risks. This approach allows companies to prioritize CAPA activities based on risk, focusing resources on issues that could have the greatest impact on product quality and patient safety.
- Leverage Data Analytics: Utilize data analytics to identify trends and patterns in quality data, such as recurring deviations or nonconformities. Advanced analytical tools can help detect issues early, enabling a more proactive CAPA approach and minimizing the chances of repeated incidents.
- Involve Cross-Functional Teams: Incorporate representatives from various departments such as manufacturing, quality assurance, and regulatory affairs in CAPA activities. This cross-functional collaboration ensures diverse perspectives are considered, leading to more comprehensive problem-solving and stronger corrective actions.
- Regular Review and Updates: Conduct periodic reviews of the CAPA system to ensure it remains aligned with current processes and regulatory expectations. Regular updates help in refining CAPA procedures and maintaining their effectiveness as the organization and its processes evolve.
- Compliance with Regulatory Requirements: Ensure the CAPA system complies with relevant regulations, including ICH Q10, FDA, and other applicable guidelines. This involves keeping documentation up-to-date, maintaining traceability, and being audit-ready. Proper documentation and adherence to regulatory standards build confidence with regulatory bodies and ensure sustained compliance.
Final Thoughts: Leveraging CAPA for Quality Excellence
CAPA is an essential component of an effective PQS, as outlined in ICH Q10. By effectively identifying, investigating, and addressing quality issues, pharmaceutical companies can ensure the safety, efficacy, and compliance of their products. The right CAPA system not only helps to prevent future problems but also provides valuable insights for process improvement and continuous learning.
By following the principles and best practices outlined in ICH Q10 and this post, pharmaceutical companies can establish a CAPA system that supports long-term success. A leading CAPA system can help to build trust with regulatory authorities, customers, and patients, ultimately enhancing the reputation and sustainability of the company.
Ultimately, CAPA is a strategic tool for ensuring product quality and safety, driving continuous improvement, and building a culture of excellence within the pharmaceutical industry.
Is your solution aligned with the ICH Q10 guidelines? We’ve created a checklist to help guide you. Download it today.